Magnesium Die Casting
Our Expertise of Magnesium Casting (Magnesium Die Casting)
We are very experienced in magnesium casting including magnesium die casting. With strong capability of casting a wide variety of magnesium steel alloys such as AZ91D, AM60B and AM50, we provide custom magnesium casting parts and components for industries and applications including automotive, food & dairy, machinery, medical, plumbing, watering, mining, petrochemical, electrical, energy, aerospace, submarine and others. We can assure you high quality magnesium castings.
For your magnesium casting and magnesium die casting needs, we can help you out with our best services.
What Is Magnesium?
Magnesium is the lightest structural material, about 1.8 grams per cubic centimetre. magnesium is the 8th most abundant element in the earth’s crust. It occurs naturally in Dolomite, Magnesite, Carnallite and Chloride (sea water). Magnesium is produced from sea water, brines and magnesium-bearing minerals which offer unlimited reserves.
Magnesium is 75% lighter than steel, 33% lighter than aluminum, offers component and feature integration and provides a high dimensional stability that improves fit and finish.
Benefits of Magnesium
- Lightest of all structural materials
- 75% lighter than steel
- 33% lighter than aluminum
- High impact resistance
- High strength to weight ratio
- Can be cast to net shape
- Excellent dimensional stability/repeatability
- Abundant material supply
- 100% recyclable
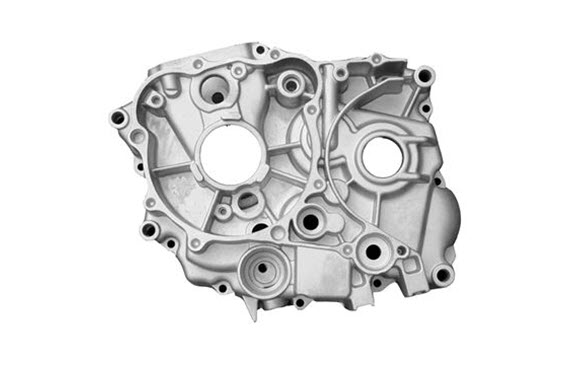
Comparison Between Magnesium and Steel
Comparing to steel, magnesium is 75% lighter, with advantages such as component consolidation/integration, significantly lower tooling costs, high heat conductivity, complicated thin-walled near net shape and superior dimensional stability/repeatability.
Comparison Between Magnesium and Plastic
Comparing to steel, magnesium is stronger, with advantages such as superior stiffness, greater energy absorbing capabilities, higher temperature applications and large thin-walled near net shape casting.
Comparison Between Magnesium and Aluminum
Comparing to aluminum, magnesium is 33% lighter, with advantages such as superior machining, large thin-walled near net shape casting, greater mechanical properties and greater general corrosion resistance.
Magnesium Alloys We Die Cast
We help our customer to select alloy based on the environment the part will function in the performance requirements of the component.
AZ91D: Most commonly used alloy for high pressure die casting. Offers good strength to weight ratio, very good corrosion resistance and excellent castability. This alloy is typically used for power-train and mechanical components where toughness is more important than deformation capability.
AM60B: Commonly used for automotive die castings for safety components such as instrument panel structures and seat frames. This alloy offers excellent ductility, energy absorbing properties, strength and castability.
AM50: With a lower aluminum content than AM60 this alloy offers a further increase in ductility but at a slightly reduced strength and a slight reduction in castability. It is typically used where the performance requirements demand elongation properties beyond that of AM60.
Notes: For applications such as power-train components where the operating temperature is above 120 degrees C (example; automatic transmission housing) there is a large selection of magnesium alloys available. These alloys are designed to operate in the higher temperatures without “creep” so that bolt tension and sealing surface flatness is maintained. Meridian recommends discussing this with our engineering group to review the options available.
Advantages of Magnesium Die Casting
- Lightest of all structural materials
- Excellent Stiffness
- Outstanding EMI and RFI shielding properties, perfect for connectors and electrical housings
- Withstands high operating temperatures
- Exceptional thin wall capability
- Good environmental corrosion resistance
- Excellent dimensional stability/repeatability
- Good finishing characteristics
- 100% recyclable
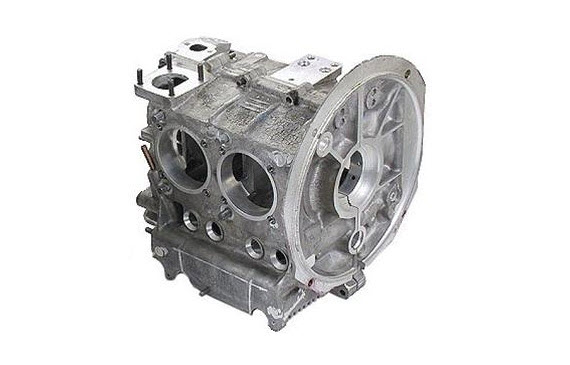
Magnesium Die Casting Material Information
Mechanical Properties | AZ91D | AM60B | AM50A |
---|---|---|---|
Ultimate Tensile Strength (Mpa) | 240 | 225 | 210 |
Yield Strength (Mpa) | 160 | 130 | 125 |
Elongation (% ub 2 in (51mm) | 3 | 8 | 10 |
Hardness (Brinell) | 70 | 65 | 60 |
Elastic Modulus (Gpa) | 45 | 45 | 45 |
Physical Properties | AZ91D | AM60B | AM50A |
---|---|---|---|
Density (g / cm³) | 1.81 | 1.80 | 1.77 |
Melting Range (F) | 815 to 1,108 | 815 to 1,139 | 815 to 1,238 |
Melting Range (C) | 435 to 598 | 435 to 615 | 435 to 620 |
Specific Heat (kJ/kg k) | 1.02 | 1.02 | 1.02 |
Thermal Conductivity (W / m – k ) | 51 | 61 | 65 |
Electrical Conductivity (MS/m) | 6.6 | 9.1 | — |
Corrosion Rate (mg/cm²/day) | 0.05 | 0.09 | 0.1 |
Secondary Operations of Magnesium Die Casting
- Painting using e-coat or powder coat processes
- Machining
How Do We Protect Against Galvanic Corrosion?
Galvanic corrosion occurs when dissimilar metal is in contact with the magnesium casting and with an electrolyte presents such as salt water. There is no issue with interior components. However for parts and components such as body, chassis or power-train castings, there is a likelihood that galvanic corrosion protection will be required. The approach is to isolate the dissimilar metals either by coating one of the components or using an isolating material as a washer to eliminate the galvanic effect.
Magnesium Casting Tooling and Prototype Options
We offers our customers several options for tooling and prototype parts depending on the intended use of the parts. With requirements of various lead times and tool life availability to meet all program schedules, tooling options include sand casting tooling, die casting tooling, rapid tooling, and soft prototype tooling.
Sources
- American Foundry Society. “Metal Casting”
- Wikipedia. “Investment Casting“, “Sand Casting“
- efunda. “Sand Casting“
- The Investment Casting Institute. “What is Investment Casting?“
- The Library of Manufacturing. “Investment Casting“
- Forging Industry Association “Forging Industry“
Our Internal Resources for Die Casting, Investment casting, Forging and Sand Casting
- Die Casting
- Aluminum Die Casting
- Zinc Die Casting
- A356 Aluminum Casting with T6 Heat Treatment
- Magnesium Die Casting
- Investment Casting
- Stainless Steel Casting
- Duplex Stainless Steel Casting
- Super Duplex Stainless Steel Casting
- Titanium Casting
- Carbon & Low Alloy Casting
- Forging
- Cold Forging
- Hot Forging
- ECO BRASS C69300 Brass Forging
- Sand Casting (Aluminum Sand Casting, Ductile Iron Sand Casting, Gray Iron Sand Casting)
- Specialty Fittings and Fasteners
- Precision CNC Machining and Secondary Operations