Zinc Die Casting
We produce zinc die casting parts from a few grams to more than 100 pounds with superior quality ready for assembly. we offer a broad range of zinc die casting surface finishing including powder coating, e-coating, shot blasting, chrome plating, and bright finish. The industries ForceBeyond serves include automotive, food dairy, machinery, medical, plumbing, watering, mining, petrochemical, electrical, energy, aerospace, submarine and others.
What Is Zinc Die Casting?
Zinc die casting is a metal casting process characterized by pressuring molten metal into the mold cavity. The mold cavity is created using two hardened tool steel molds that are machined to the net shape or near net shape of the zinc die casting parts. Zinc die casting process allows products to be made with high degree of accuracy and repeatability. The Zinc die casting process can also produce fine details such as textured surfaces or names without requiring further processing.
How are Zinc Die Castings Made?
Steel dies capable of producing tens of thousands of zinc castings in quick succession must be made in at least two sections to allow the castings to be removed. These parts are firmly mounted in the machine and are arranged so that one is stationary (fixed die half) and the other one is movable (injector die half). To begin the casting cycle, the two mold halves are clamped together by a die-casting machine. Molten zinc alloy is injected into the mold cavity and rapidly solidified. The mold half is opened and the zinc casting is ejected. Zinc die casting molds can be simple or complicated, with movable slides, cores or other parts, depending on the complexity of the casting.
To date, the complete cycle of zinc die casting has been the fastest cycle to produce precision zinc parts. This is in stark contrast to sand casting, which requires new sand molds for each casting. Although the permanent mold process uses iron or steel molds instead of sand, it is much slower and less precise than zinc die castings.
Watch the video of our zinc die casting facility to learn how zinc die castings are made. Video also available on youtube.com.
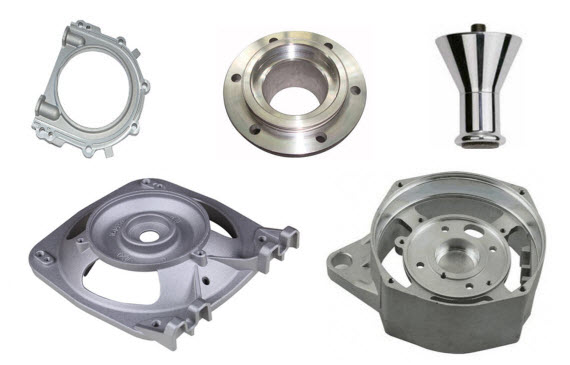
Advantages of Zinc Die Casting
- Great tool life
- Precision tolerance
- Superior thermal conductivity
- Fast cycle time
- Corrosion resistance
- Superior for decorative finishing
- Low energy cost
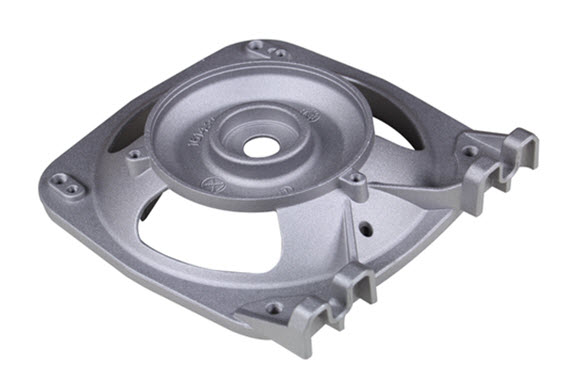
Zinc Die Casting Material Information
Material | Tensile Strength (Mpa) | Thermal Conductivity (W/mK) | Features |
---|---|---|---|
ZAMAK 2 | 359 | 105 |
|
ZAMAK 3 | 283 | 113 |
|
ZAMAK 5 | 328 | 109 |
|
ZA 8 | 374 | 115 |
|
Secondary Operations of Zinc Die Casting We Offer
- High precision CNC machining, milling, drilling, tapping, e-coating, anodizing
- Painting, sanding, shot blasting, powder coating, chrome plating
Sources
- American Foundry Society. “Metal Casting”
- Wikipedia. “Investment Casting“, “Sand Casting“
- efunda. “Sand Casting“
- The Investment Casting Institute. “What is Investment Casting?“
- The Library of Manufacturing. “Investment Casting“
- Forging Industry Association “Forging Industry“
Our Internal Resources for Die Casting, Investment casting, Forging and Sand Casting
- Die Casting
- Aluminum Die Casting
- Zinc Die Casting
- A356 Aluminum Casting with T6 Heat Treatment
- Magnesium Die Casting
- Investment Casting
- Stainless Steel Casting
- Duplex Stainless Steel Casting
- Super Duplex Stainless Steel Casting
- Titanium Casting
- Carbon & Low Alloy Casting
- Forging
- Cold Forging
- Hot Forging
- ECO BRASS C69300 Brass Forging
- Sand Casting (Aluminum Sand Casting, Ductile Iron Sand Casting, Gray Iron Sand Casting)
- Specialty Fittings and Fasteners
- Precision CNC Machining and Secondary Operations